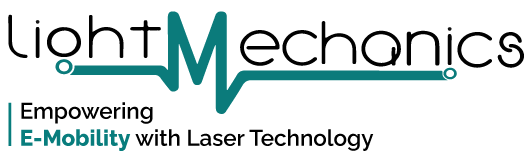
Want to explore the laser technology best suited for your application? Send us your samples for a FREE trials!
Contact us nowAs batteries are manufactured at a very high rate, sometimes well over 10 per second, the use of resistance welders or mechanical fasteners is not always viable. Light Mechanics Fiber Lasers can optically match the speed of the moving cell and spot weld without contact, electrode wear and tear or electrode sticking.
Low heat input spot and seam welding has been achieved with flash lamp-pumped solid state lasers for many years. It is now possible to replicate their performance with a zero maintenance fiber laser. These new fiber lasers have identical pulse durations and pulse energies and similar peak power capabilities to YAG lasers. The ability to focus to a sub 50 micron spot size enables the fiber laser to achieve the necessary power densities required to couple into these reflective materials. In addition the heat conduction of the materials stabilizes the weld from overheating due to the highly localized power density and also spread the weld volume to ease the potential issues of seam tracking with such as small spot size. These makes it ideal for battery manufacturing applications such as seam sealing and pack manufacture.
The rapid growth in market share of fiber lasers demonstrates that their benefits are now well recognized but until recently only continuous wave (CW) or CW modulated lasers were available for welding. Although pulsed laser welding could be achieved by modulating a continuous fiber laser beam, average power was substituting for peak power and a more costly higher average power laser was required to achieve the necessary multi-joule pulses. Laser welding has quickly become one of the most important processes for the dissimilar metal welding of lithium-ion batteries. Given that there are several dissimilar metals involved, and also given that the industry continues to see exponential growth, a process that is both cost-effective, efficient and fast was required. The challenge with this application is that welding dissimilar metals often has issues with heat input and formation of brittle inter metallic phases. Using Fiber Lasers for such an application reduces the heat input and the heat-affected zone to further reduce cycle time.
Laser welding uses a focused laser beam as a point source of energy to create localised heating to join parts together. Because of the small cross section of the laser beam and its energy concentration, narrow and deep welds can be made with a high welding speed. Also, because of the narrow welds and high welding speed, the process generates a low level of heat in the assembly during welding, which is important for battery tab welding, as the chemicals inside the batteries are very heat sensitive. When welding a tab to a terminal, generally, the tab should be thinner than the battery cell casing terminal. Process parameters need to be controlled to provide weld strength and conductivity without penetrating the battery case/can. Other applications include sealing of the battery casing for prismatic cells, and joining of tab-to-bus bar and bus bar-to-bus bar. Additional benefits of using Fiber Lasers are that they are able to produce accurate, controllable, consistent and repeatable welds. This process has become one of the most useful for dozens of industries around the world. Its use with batteries sees it having a big impact in the electronics industry, and it also plays a part in the automotive, aerospace, construction, medical, shipping and food processing industries, among others.