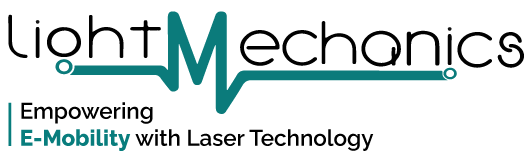
Want to explore the laser technology best suited for your application? Send us your samples for a FREE trials!
Contact us nowThe Li-ion batteries are complex assemblies of multiple layers of several materials like copper, nickel, aluminium, nickel plated copper, stainless steel etc. in a wide range of thicknesses ranging from 0.10mm – 5mm. The manufacturing of such packs involves welding a large number of connections including joints between dissimilar materials. As batteries are manufactured at a very high rate, sometimes well over 10 per second, the use of resistance welders or mechanical fasteners is not always viable, resulting in laser welding becoming a technology of choice where matching cycle times becomes a crucial factor to be considered.
At Light Mechanics, we manufacture laser welding machines for various applications in Battery manufacturing and assembly lines.
For battery welding applications both CW (Continuous Wave) and QCW (Quasi Continuous Wave) lasers are used. The manufacturing or the joining needs are determined by the pack size, tab and terminal material along with the type and thickness of busbars. A clean understanding of application is required to implement the best laser welding solution suitable for the requirement.
Our “flashweld” battery welding systems comes with high quality laser, multi axis laser welding head with wobble option, Industrial chiller, panel AC, Fume Extractor, Class 1 enclosures with pneumatics, camera for weld positioning, post process weld inspection systems, XYZ gantry, conveyors to name a few.